Managing inventory efficiently is crucial for any business that deals with physical products. Whether you’re a retailer, manufacturer, or warehouse manager, performing regular inventory audits ensures that your stock levels match the recorded data. A well-structured Inventory Audit Checklist is the foundation of a smooth and accurate audit process.
In this article, we will dive deep into the Inventory Audit Checklist, its essential components, and why it’s a must-have tool for maintaining inventory accuracy. We’ll also share best practices, potential opportunities for improvement, and a sample template to get you started.
What Is an Inventory Audit Checklist?
Click to buy Inventory Audit
An Inventory Audit Checklist is a document or template that helps businesses track the physical count and condition of their inventory. It serves as a systematic tool for identifying discrepancies between actual stock and recorded inventory, ensuring that businesses maintain accurate records.
This checklist can include tasks such as verifying item conditions, reconciling physical counts with inventory systems, ensuring proper storage practices, and much more. By organizing these tasks in a checklist format, businesses can ensure consistency and thoroughness in every audit.
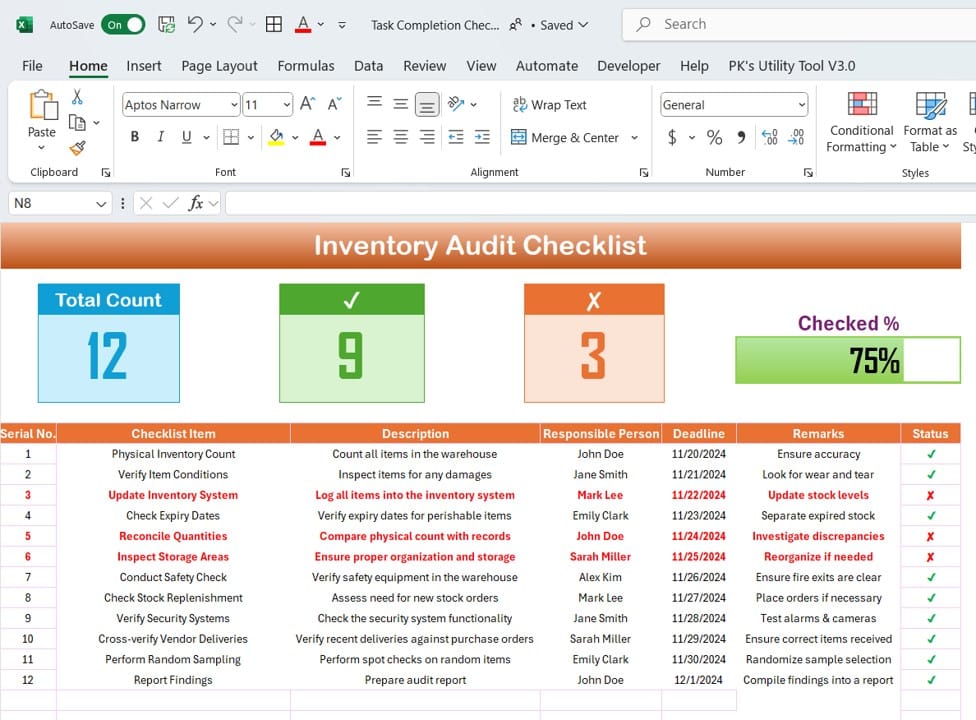
Click to buy Inventory Audit
Key Features of an Inventory Audit Checklist
The Inventory Audit Checklist typically consists of two main sections:
- Checklist Table: This is where the tasks and responsibilities are listed.
- Progress Tracking Section: A section to track completion, such as the total number of tasks completed, the percentage of tasks checked, and any discrepancies found.
Below is an example of what a typical Inventory Audit Checklist might look like:
- Improved Accuracy: Regular audits help identify discrepancies between recorded and actual stock levels. By following a checklist, you ensure that every aspect of the inventory is checked, reducing the chances of human error.
- Efficiency in Inventory Management: An audit checklist ensures that all the necessary steps are followed, and no task is overlooked. This leads to a faster, more organized audit process, saving valuable time for the staff.
- Better Accountability: By assigning specific tasks to responsible persons and setting deadlines, the checklist promotes accountability. Team members know exactly what they need to do and by when.
- Streamlined Reporting: The inventory audit checklist facilitates easier reporting by maintaining a clear record of completed tasks, findings, and discrepancies. This makes it simple to compile audit reports and make informed business decisions.
- Compliance with Regulations: Certain industries require regular inventory audits to comply with regulations. Using a checklist ensures that all required tasks are covered, which can be important during audits by regulatory bodies.
Opportunities for Improvement in Inventory Audits
While the Inventory Audit Checklist is a powerful tool, there are always opportunities for improvement in any process. Here are a few ways you can improve your inventory audit procedures:
- Integrating Technology: Modernizing your inventory audit process with technology can greatly enhance accuracy and efficiency. Consider using inventory management software that integrates with your checklist. This allows for real-time updates, automated reporting, and data analysis.
- Regularly Updating the Checklist: As your business grows or your inventory system evolves, you must ensure that your checklist stays relevant. Regularly review the checklist to make sure it covers all essential tasks and reflects any changes in your inventory system or process.
- Automating Data Entry: Manual data entry can slow down the auditing process. Consider integrating barcode scanning or RFID systems with your inventory checklist to automate data collection and update inventory counts automatically.
- Training and Development: Ensuring your staff is trained in how to properly conduct inventory audits can significantly improve the accuracy and efficiency of your audits. Regularly provide training on new processes, tools, and best practices.
- Best Practices for Inventory Audits: To ensure the success of your inventory audits, follow these best practices:
- Conduct Regular Audits: Do not wait until the end of the year or the end of a fiscal period to perform an inventory audit. Conduct regular audits (monthly or quarterly) to maintain accurate inventory levels throughout the year.
- Assign Clear Responsibilities: Make sure each task in the checklist is assigned to a specific person. This ensures accountability and prevents confusion during the audit process.
- Set Realistic Deadlines: Setting reasonable deadlines ensures that tasks are completed on time, and it gives the team enough time to thoroughly audit each area.
- Use a Clear and Simple Checklist: The checklist should be easy to understand and user-friendly. Avoid jargon and ensure that every team member can easily follow the checklist.
- Perform Spot Checks: In addition to full inventory audits, consider doing random spot checks of inventory. This adds an extra layer of accuracy and ensures that your team is consistently maintaining inventory standards.
- Track Performance and Results: Track the completion rate of the checklist, and analyze the results. If discrepancies are found, take corrective actions immediately to prevent future issues.
Conclusion
An Inventory Audit Checklist is an indispensable tool for businesses looking to maintain accurate inventory levels, improve efficiency, and ensure compliance with regulations. By following the checklist and incorporating best practices, you can minimize errors, improve accountability, and streamline your inventory audit process.
Remember, the key to a successful inventory audit lies in preparation, consistency, and continuous improvement. Using technology, assigning responsibilities, and regularly reviewing your checklist will help you stay ahead and maintain optimal inventory management.
Frequently Asked Questions (FAQs)
Q. What Is the Purpose of an Inventory Audit Checklist?
The purpose of an inventory audit checklist is to track the status of inventory items, ensure accuracy, and identify discrepancies between actual stock and recorded inventory. It helps streamline the auditing process and ensures thorough checks are made.
Q. How Often Should an Inventory Audit Be Performed?
Ideally, inventory audits should be performed regularly, such as monthly or quarterly. The frequency may vary depending on the size of your business and inventory, but regular audits help maintain accuracy throughout the year.
Q. Can I Use Inventory Audit Checklists in Excel?
Yes, Excel is a great tool for creating inventory audit checklists. You can easily create columns for task descriptions, responsible persons, deadlines, and status updates. Additionally, Excel allows you to use checkboxes, making it easy to track completed tasks.
Q. How Do I Assign Responsibilities in an Inventory Audit Checklist?
In an inventory audit checklist, you can assign specific tasks to team members by listing their names in the “Responsible Person” column for each checklist item. This ensures accountability and prevents confusion during the audit process.
Q. What Are the Best Practices for Inventory Audits?
Some best practices for inventory audits include conducting regular audits, assigning clear responsibilities, setting realistic deadlines, and using a simple, easy-to-understand checklist. Tracking performance and performing spot checks also help ensure accuracy.
Visit our YouTube channel to learn step-by-step video tutorials
Click to buy Inventory Audit